Dây chuyền phun hóa chất Downhole-Tại sao chúng thất bại?Kinh nghiệm, Thách thức và Áp dụng Phương pháp Kiểm tra Mới
Bản quyền 2012, Hiệp hội Kỹ sư Dầu khí
trừu tượng
Statoil đang vận hành một số lĩnh vực áp dụng việc phun liên tục chất ức chế cáu cặn.Mục tiêu là để bảo vệ ống trên và van an toàn khỏi(Ba/Sr)SO4hoặcCaCO;quy mô, trong những trường hợp mà việc thu hẹp quy mô có thể khó khăn và tốn kém để thực hiện một cách thường xuyên, ví dụ như liên kết các lĩnh vực dưới biển.
Bơm liên tục chất ức chế đóng cặn vào hố xuống là một giải pháp thích hợp về mặt kỹ thuật để bảo vệ ống trên và van an toàn trong các giếng có khả năng đóng cặn bên trên máy đóng gói sản xuất;đặc biệt là trong các giếng không cần phải siết chặt thường xuyên do khả năng đóng cặn ở khu vực gần giếng.
Việc thiết kế, vận hành và bảo trì các dây chuyền phun hóa chất đòi hỏi phải tập trung hơn vào việc lựa chọn vật liệu, kiểm định và giám sát hóa chất.Áp suất, nhiệt độ, chế độ dòng chảy và hình học của hệ thống có thể gây ra những thách thức đối với hoạt động an toàn.Những thách thức đã được xác định trong các đường ống tiêm dài vài km từ cơ sở sản xuất đến mẫu dưới biển và trong các van phun ở dưới giếng.
Kinh nghiệm thực địa cho thấy sự phức tạp của các hệ thống phun liên tục hạ cấp liên quan đến các vấn đề kết tủa và ăn mòn sẽ được thảo luận.Các nghiên cứu trong phòng thí nghiệm và ứng dụng các phương pháp mới để đánh giá chất lượng hóa học được trình bày.Các nhu cầu cho các hành động đa ngành được giải quyết.
Giới thiệu
Statoil đang vận hành một số mỏ áp dụng phương pháp bơm hóa chất liên tục vào lỗ khoan.Điều này chủ yếu liên quan đến việc tiêm chất ức chế cặn (SI) trong đó mục tiêu là bảo vệ ống trên và van an toàn lỗ xả (DHSV) khỏi (Ba/Sr) SO4hoặcCaCO;tỉ lệ.Trong một số trường hợp, chất phá vỡ nhũ tương được bơm vào lỗ khoan để bắt đầu quá trình phân tách càng sâu trong giếng càng tốt ở nhiệt độ tương đối cao.
Phun liên tục chất ức chế đóng cặn xuống hố khoan là một giải pháp thích hợp về mặt kỹ thuật để bảo vệ phần trên của các giếng có khả năng đóng cặn bên trên máy đóng gói sản xuất.Việc phun liên tục có thể được khuyến nghị, đặc biệt là trong các giếng không cần phải ép do khả năng đóng cặn thấp ở gần giếng;hoặc trong những trường hợp mà việc ép quy mô có thể khó khăn và tốn kém để thực hiện một cách thường xuyên, ví dụ như liên kết các mỏ dưới biển.
Statoil đã có nhiều kinh nghiệm về việc phun hóa chất liên tục lên các hệ thống trên đỉnh và các mẫu dưới biển nhưng thách thức mới là đưa điểm phun vào sâu hơn nữa trong giếng.Việc thiết kế, vận hành và bảo trì các dây chuyền phun hóa chất đòi hỏi phải tập trung nhiều hơn vào một số chủ đề;chẳng hạn như lựa chọn vật liệu, chất lượng hóa học và giám sát.Áp suất, nhiệt độ, chế độ dòng chảy và hình học của hệ thống có thể gây ra những thách thức đối với hoạt động an toàn.Đã xác định được những thách thức đối với các đường dây phun dài (vài km) từ cơ sở sản xuất đến mẫu dưới biển và vào các van phun ở dưới giếng;Hình.1.Một số hệ thống tiêm đã hoạt động theo kế hoạch, trong khi những hệ thống khác không hoạt động vì nhiều lý do.Một số phát triển lĩnh vực mới được lên kế hoạch để bơm hóa chất xuống hố (DHCI);Tuy nhiên;một số trường hợp thiết bị chưa được kiểm định đầy đủ.
Ứng dụng của DHCPI là một nhiệm vụ phức tạp.Nó liên quan đến việc hoàn thiện và thiết kế giếng, hóa chất trong giếng, hệ thống bên trên và hệ thống định lượng hóa chất của quy trình bên trên.Hóa chất sẽ được bơm từ trên đỉnh qua dây phun hóa chất đến thiết bị hoàn thiện và xuống giếng.Do đó, trong việc lập kế hoạch và thực hiện loại dự án này, sự hợp tác giữa một số ngành là rất quan trọng.Các cân nhắc khác nhau phải được đánh giá và giao tiếp tốt trong quá trình thiết kế là rất quan trọng.Các kỹ sư quy trình, kỹ sư dưới biển và kỹ sư hoàn thiện có liên quan, xử lý các chủ đề về hóa học giếng khoan, lựa chọn vật liệu, đảm bảo dòng chảy và quản lý hóa chất sản xuất.Những thách thức có thể là vua súng hóa học hoặc ổn định nhiệt độ, ăn mòn và trong một số trường hợp là hiệu ứng chân không do áp suất cục bộ và hiệu ứng dòng chảy trong dây chuyền phun hóa chất.Ngoài ra, các điều kiện như áp suất cao, nhiệt độ cao, tốc độ khí cao, khả năng đóng cặn cao,khoảng cách xa và điểm phun sâu trong giếng, đưa ra những thách thức và yêu cầu kỹ thuật khác nhau đối với hóa chất được tiêm và van phun.
Tổng quan về các hệ thống DHCI được cài đặt trong các hoạt động của Statoil cho thấy rằng kinh nghiệm không phải lúc nào cũng thành công Bảng 1. Tuy nhiên, việc lập kế hoạch cải tiến thiết kế hệ thống phun, chất lượng hóa chất, vận hành và bảo trì đang được thực hiện.Các thách thức khác nhau giữa các lĩnh vực và vấn đề không nhất thiết là bản thân van phun hóa chất không hoạt động.
Trong những năm qua, một số thách thức liên quan đến các dây chuyền phun hóa chất hạ cấp đã được trải qua.Trong bài viết này, một số ví dụ được đưa ra từ những kinh nghiệm này.Bài viết thảo luận về những thách thức và biện pháp thực hiện để giải quyết các vấn đề liên quan đến dây chuyền DHCI.Hai trường hợp lịch sử được đưa ra;một về ăn mòn và một về vua súng hóa học.Kinh nghiệm thực địa cho thấy sự phức tạp của các hệ thống phun liên tục hạ cấp liên quan đến các vấn đề kết tủa và ăn mòn sẽ được thảo luận.
Các nghiên cứu trong phòng thí nghiệm và áp dụng các phương pháp mới để xác định chất lượng hóa học cũng được xem xét;cách bơm hóa chất, khả năng mở rộng quy mô và phòng ngừa, ứng dụng thiết bị phức tạp và cách hóa chất sẽ ảnh hưởng đến hệ thống bên trên khi hóa chất được sản xuất trở lại.Chấp nhận các tiêu chí cho ứng dụng hóa chất liên quan đến các vấn đề môi trường, hiệu quả, khả năng lưu trữ trên đỉnh, tốc độ bơm, liệu có thể sử dụng máy bơm hiện tại hay không, v.v. Các khuyến nghị kỹ thuật phải dựa trên khả năng tương thích của chất lỏng và hóa học, khả năng phát hiện dư lượng, khả năng tương thích của vật liệu, thiết kế rốn dưới biển, hệ thống định lượng hóa chất và các vật liệu xung quanh các đường này.Hóa chất có thể cần phải được ức chế hydrat để ngăn không cho khí xâm nhập vào đường ống tiêm và hóa chất không được đóng băng trong quá trình vận chuyển và bảo quản.Trong các hướng dẫn nội bộ hiện có, có một danh sách kiểm tra các hóa chất có thể được áp dụng tại mỗi điểm trong hệ thống Các đặc tính vật lý như độ nhớt rất quan trọng.Hệ thống phun có thể ngụ ý khoảng cách 3-50 km của dòng chảy dưới đáy biển rốn và 1-3 km xuống giếng.Do đó, sự ổn định nhiệt độ cũng rất quan trọng.Đánh giá các tác động hạ lưu, ví dụ như trong các nhà máy lọc dầu cũng có thể phải được xem xét.
Hệ thống phun hóa chất downhole
Lợi ích chi phí
Việc bơm liên tục chất ức chế cáu cặn vào hố xuống để bảo vệ DHS Vor ống sản xuất có thể tiết kiệm chi phí so với việc ép giếng bằng chất ức chế cáu cặn.Ứng dụng này làm giảm khả năng hư hỏng hình thành so với các phương pháp xử lý ép quy mô, giảm khả năng xảy ra các vấn đề về quy trình sau khi ép quy mô và mang lại khả năng kiểm soát tốc độ phun hóa chất từ hệ thống phun phía trên.Hệ thống phun cũng có thể được sử dụng để bơm các hóa chất khác liên tục xuống hố và do đó có thể làm giảm các thách thức khác có thể xảy ra ở phía sau nhà máy xử lý.
Một nghiên cứu toàn diện đã được thực hiện để phát triển chiến lược quy mô hạ cấp của Oseberg S hoặc trường.Mối quan tâm chính về quy mô là CaCO;đóng cặn ở ống trên và có thể xảy ra lỗi DHSV.Oseberg S hoặc xem xét chiến lược quản lý quy mô đã kết luận rằng trong khoảng thời gian ba năm, DHCI là giải pháp tiết kiệm chi phí nhất trong các giếng nơi các dây chuyền phun hóa chất đang hoạt động.Yếu tố chi phí chính liên quan đến kỹ thuật ép quy mô cạnh tranh là dầu hoãn lại chứ không phải chi phí hóa chất/vận hành.Đối với ứng dụng của chất ức chế cáu cặn trong quá trình nâng khí, yếu tố chính ảnh hưởng đến chi phí hóa chất là tốc độ nâng khí cao dẫn đến nồng độ SI cao, do nồng độ phải được cân bằng với tốc độ nâng khí để tránh tình trạng súng hóa chất.Đối với hai giếng trên Oseberg S hoặc có các dòng DHC I hoạt động tốt, tùy chọn này đã được chọn để bảo vệ DHS V khỏi CaCO;mở rộng quy mô.
Hệ thống phun liên tục và van
Các giải pháp hoàn thiện hiện tại sử dụng hệ thống phun hóa chất liên tục phải đối mặt với những thách thức trong việc ngăn ngừa tắc nghẽn các đường mao dẫn.Thông thường, hệ thống tiêm bao gồm một đường mao dẫn, đường kính ngoài (OD) 1/4” hoặc 3/8”, được nối với một ống góp bề mặt, được đưa qua và nối với giá treo ống ở mặt hình khuyên của ống.Đường mao dẫn được gắn vào đường kính ngoài của ống sản xuất bằng các kẹp cổ ống đặc biệt và chạy bên ngoài ống xuống tận trục gá phun hóa chất.Theo truyền thống, trục gá được đặt ngược dòng của DHS V hoặc sâu hơn trong giếng với mục đích giúp hóa chất được bơm vào có đủ thời gian phân tán và đặt hóa chất ở những nơi có thách thức.
Tại van phun hóa chất, Hình 2, một hộp nhỏ có đường kính khoảng 1,5” chứa các van một chiều ngăn không cho chất lỏng trong giếng đi vào đường ống mao dẫn.Nó chỉ đơn giản là một con búp bê nhỏ cưỡi trên lò xo.Lực lò xo thiết lập và dự đoán áp suất cần thiết để mở móc khóa ra khỏi ghế đệm.Khi hóa chất bắt đầu chảy, poppet được nhấc ra khỏi ghế và mở van kiểm tra.
Cần phải lắp đặt hai van kiểm tra.Một van là rào cản chính ngăn không cho chất lỏng trong giếng đi vào đường mao dẫn.Điều này có áp suất mở tương đối thấp (2-15bars). Nếu áp suất thủy tĩnh bên trong đường mao dẫn nhỏ hơn áp suất trong lòng giếng, chất lỏng trong giếng sẽ cố gắng đi vào trong đường mao dẫn.Van một chiều khác có áp suất mở không điển hình là 130-250 bar và được gọi là hệ thống ngăn chặn ống chữ U.Van này ngăn không cho hóa chất bên trong đường mao dẫn chảy tự do vào giếng nếu áp suất thủy tĩnh bên trong đường ống mao quản lớn hơn áp suất lỗ giếng tại điểm phun hóa chất bên trong ống sản xuất.
Ngoài hai van kiểm tra, thường có một bộ lọc trong dòng, mục đích của việc này là để đảm bảo rằng không có mảnh vụn nào có thể gây nguy hiểm cho khả năng bịt kín của hệ thống van kiểm tra.
Kích thước của các van kiểm tra được mô tả là khá nhỏ và độ sạch của chất lỏng được bơm vào là điều cần thiết cho chức năng hoạt động của chúng.Người ta tin rằng các mảnh vụn trong hệ thống có thể được xả sạch bằng cách tăng tốc độ dòng chảy bên trong đường ống mao dẫn, do đó các van kiểm tra sẽ mở ra một cách có chủ ý.
Khi van một chiều mở ra, áp suất dòng chảy giảm nhanh chóng và lan truyền lên đường mao dẫn cho đến khi áp suất tăng trở lại.Sau đó, van một chiều sẽ đóng lại cho đến khi dòng hóa chất tích tụ đủ áp suất để mở van;kết quả là dao động áp suất trong hệ thống van kiểm tra.Áp suất mở của hệ thống van kiểm tra càng cao thì diện tích dòng chảy được thiết lập khi van kiểm tra mở ra càng ít và hệ thống cố gắng đạt được các điều kiện cân bằng.
Các van phun hóa chất có áp suất mở tương đối thấp;và nếu áp suất đường ống tại điểm đầu vào hóa chất trở nên nhỏ hơn tổng áp suất thủy tĩnh của các hóa chất bên trong đường mao dẫn cộng với áp suất mở van kiểm tra, thì gần như chân không hoặc chân không sẽ xảy ra ở phần trên của đường mao dẫn.Khi quá trình bơm hóa chất dừng lại hoặc lưu lượng hóa chất thấp, điều kiện gần chân không sẽ bắt đầu xảy ra ở phần trên cùng của đường ống mao dẫn.
Mức độ chân không phụ thuộc vào áp suất lỗ khoan, trọng lượng riêng của hỗn hợp hóa chất được bơm vào được sử dụng bên trong đường ống mao dẫn, áp suất mở của van kiểm tra tại điểm phun và lưu lượng của hóa chất bên trong đường ống mao dẫn.Các điều kiện giếng sẽ thay đổi trong suốt thời gian tồn tại của trường và tiềm năng chân không do đó cũng sẽ thay đổi theo thời gian.Điều quan trọng là phải nhận thức được tình hình này để có sự cân nhắc và đề phòng đúng đắn trước khi những thách thức dự kiến xảy ra.
Cùng với tốc độ tiêm thấp, thông thường các dung môi được sử dụng trong các loại ứng dụng này đang bay hơi gây ra các hiệu ứng chưa được khám phá đầy đủ.Những hiệu ứng này là súng vương hoặc kết tủa chất rắn, ví dụ như polyme, khi dung môi bay hơi.
Hơn nữa, các tế bào điện có thể được hình thành trong giai đoạn chuyển tiếp giữa bề mặt chất lỏng của hóa chất và pha khí gần chân không chứa đầy hơi ở trên.Điều này có thể dẫn đến ăn mòn rỗ cục bộ bên trong đường ống mao dẫn do tính ăn mòn của hóa chất tăng lên trong những điều kiện này.Các mảnh hoặc tinh thể muối được hình thành như một lớp màng bên trong đường mao dẫn khi phần bên trong của nó khô đi có thể làm tắc nghẽn hoặc bịt kín đường mao dẫn.
triết lý rào cản tốt
Khi thiết kế các giải pháp mạnh mẽ cho giếng, Statoil yêu cầu phải luôn đảm bảo an toàn cho giếng trong suốt vòng đời của giếng.Do đó, Statoil yêu cầu phải có hai thanh chắn giếng độc lập còn nguyên vẹn.Hình 3 cho thấy sơ đồ rào chắn giếng không điển hình, trong đó màu xanh lam đại diện cho đường bao rào chắn giếng chính;trong trường hợp này là ống sản xuất.Màu đỏ đại diện cho phong bì hàng rào thứ cấp;vỏ bọc.Ở phía bên trái trong bản phác thảo, việc tiêm hóa chất được biểu thị bằng một đường màu đen với điểm tiêm vào ống sản xuất trong khu vực được đánh dấu màu đỏ (hàng rào thứ cấp).Bằng cách đưa các hệ thống phun hóa chất vào giếng, cả rào cản chính và phụ của giếng đều bị nguy hiểm.
Trường hợp lịch sử về ăn mòn
Chuỗi sự kiện
Việc phun hóa chất ức chế cáu cặn vào lỗ khoan đã được áp dụng vào một mỏ dầu do Statoil vận hành trên Thềm lục địa Na Uy.Trong trường hợp này, chất ức chế cáu cặn được áp dụng ban đầu đủ điều kiện để ứng dụng trên bề mặt và dưới đáy biển.Việc hoàn thiện giếng được thực hiện sau khi lắp đặt DHCIpointat2446mMD, Hình 3.Quá trình bơm chất ức chế đóng cặn bên trên xuống lỗ được bắt đầu mà không cần thử nghiệm thêm hóa chất.
Sau một năm hoạt động, các rò rỉ trong hệ thống phun hóa chất đã được quan sát thấy và các cuộc điều tra đã bắt đầu.Sự rò rỉ có ảnh hưởng bất lợi đến các rào cản giếng.Các sự kiện tương tự cũng xảy ra đối với một số giếng và một số giếng đã phải đóng cửa trong khi cuộc điều tra đang diễn ra.
Các ống sản xuất đã được kéo và nghiên cứu chi tiết.Sự ăn mòn chỉ giới hạn ở một bên của ống và một số khớp nối ống bị ăn mòn đến mức thực sự có lỗ xuyên qua chúng.Thép mạ crôm 3% dày khoảng 8,5 mm đã bị phân hủy trong vòng chưa đầy 8 tháng.Sự ăn mòn chủ yếu xảy ra ở phần trên cùng của giếng, từ đầu giếng xuống khoảng 380m MD, và các mối nối ống bị ăn mòn tồi tệ nhất được tìm thấy ở khoảng 350m MD.Dưới độ sâu này, ít hoặc không có hiện tượng ăn mòn nào được quan sát thấy, nhưng rất nhiều mảnh vụn được tìm thấy trên đường kính ngoài của ống.
Vỏ 9-5/8'' cũng được cắt và kéo và quan sát thấy các hiệu ứng tương tự;với sự ăn mòn ở phần trên của giếng chỉ ở một bên.Rò rỉ gây ra là do vỡ phần yếu của vỏ.
Vật liệu dây chuyền phun hóa chất là Hợp kim 825.
Trình độ chuyên môn hóa học
Tính chất hóa học và thử nghiệm ăn mòn là trọng tâm quan trọng trong việc xác định chất lượng của chất ức chế cáu cặn và chất ức chế cáu cặn thực tế đã được đánh giá đủ điều kiện và được sử dụng trong các ứng dụng trên mặt đất và dưới đáy biển trong vài năm.Lý do áp dụng hóa chất hạ lỗ thực tế là do các đặc tính môi trường được cải thiện bằng cách thay thế hóa chất hạ cấp hiện có. Tuy nhiên, chất ức chế cáu cặn chỉ được sử dụng ở nhiệt độ bề mặt xung quanh và đáy biển (4-20℃).Khi được bơm vào giếng, nhiệt độ của hóa chất có thể lên tới 90℃, nhưng không có thử nghiệm nào khác được thực hiện ở nhiệt độ này.
Các thử nghiệm ăn mòn ban đầu đã được thực hiện bởi nhà cung cấp hóa chất và kết quả cho thấy 2-4mm/năm đối với thép carbon ở nhiệt độ cao.Trong giai đoạn này, năng lực kỹ thuật vật chất của người vận hành đã có sự tham gia tối thiểu.Các thử nghiệm mới sau đó đã được người vận hành thực hiện cho thấy rằng chất ức chế cáu cặn có tính ăn mòn cao đối với vật liệu trong ống sản xuất và vỏ bọc sản xuất, với tốc độ ăn mòn vượt quá 70mm/năm.Vật liệu dây chuyền phun hóa chất Hợp kim 825 chưa được thử nghiệm với chất ức chế đóng cặn trước khi tiêm.Nhiệt độ giếng có thể đạt tới 90℃ và các thử nghiệm thích hợp phải được thực hiện trong những điều kiện này.
Cuộc điều tra cũng tiết lộ rằng chất ức chế quy mô dưới dạng dung dịch cô đặc có độ pH <3,0.Tuy nhiên, độ pH đã không được đo.Sau đó, độ pH đo được cho thấy giá trị pH rất thấp 0-1.Điều này minh họa sự cần thiết của các phép đo và xem xét vật liệu bên cạnh các giá trị pH nhất định.
Giải thích kết quả
Đường phun (Hình 3) được xây dựng để tạo ra áp suất thủy tĩnh của chất ức chế cáu cặn vượt quá áp suất trong giếng tại điểm phun.Chất ức chế được bơm vào ở áp suất cao hơn áp suất tồn tại trong giếng.Điều này dẫn đến hiệu ứng ống chữ U khi đóng giếng.Van sẽ luôn mở với áp suất trong đường phun cao hơn trong giếng.Do đó, hiện tượng chân không hoặc bay hơi trong đường ống tiêm có thể xảy ra.Tốc độ ăn mòn và nguy cơ rỗ khí là lớn nhất trong vùng chuyển tiếp khí/lỏng do dung môi bay hơi.Các thí nghiệm trong phòng thí nghiệm được thực hiện trên phiếu giảm giá đã xác nhận lý thuyết này.Tại các giếng bị rò rỉ, tất cả các lỗ trong đường phun hóa chất đều nằm ở phần trên của đường phun hóa chất.
Hình 4 cho thấy hình ảnh của dây chuyền DHC I bị ăn mòn rỗ đáng kể.Sự ăn mòn nhìn thấy trên đường ống sản xuất bên ngoài cho thấy sự tiếp xúc cục bộ của chất ức chế cáu cặn từ điểm rò rỉ rỗ khí.Nguyên nhân rò rỉ là do ăn mòn rỗ bởi hóa chất có tính ăn mòn cao và rò rỉ qua đường phun hóa chất vào vỏ máy sản xuất.Chất ức chế đóng cặn được phun từ đường ống mao dẫn có rỗ lên vỏ và ống dẫn và xảy ra rò rỉ.Bất kỳ hậu quả thứ cấp nào của rò rỉ trong đường ống tiêm đã không được xem xét.Người ta đã kết luận rằng sự ăn mòn của vỏ và ống là kết quả của các chất ức chế cáu cặn cô đặc cầu nguyện từ đường mao dẫn bị rỗ trên vỏ và ống, Hình 5.
Trong trường hợp này đã thiếu sự tham gia của các kỹ sư năng lực vật liệu.Tính ăn mòn của hóa chất trên dây chuyền DHCI chưa được thử nghiệm và các tác động phụ do rò rỉ chưa được đánh giá;chẳng hạn như liệu các vật liệu xung quanh có thể chịu được việc tiếp xúc với hóa chất hay không.
Trường hợp lịch sử của vua súng hóa học
Chuỗi sự kiện
Chiến lược ngăn ngừa cáu cặn cho mỏ HP HT là bơm liên tục chất ức chế cáu cặn ngược dòng van an toàn lỗ xả.Khả năng đóng cặn canxi cacbonat nghiêm trọng đã được xác định trong giếng.Một trong những thách thức là nhiệt độ cao, tỷ lệ sản xuất khí và nước ngưng cao kết hợp với tỷ lệ sản xuất nước thấp.Mối quan tâm bằng cách tiêm chất ức chế cáu cặn là dung môi sẽ bị loại bỏ do tốc độ sản xuất khí cao và lượng hóa chất súng phun sẽ xảy ra tại điểm phun ngược dòng của van an toàn trong giếng, Hình 1.
Trong quá trình đánh giá chất lượng của chất ức chế cáu cặn, trọng tâm là tính hiệu quả của sản phẩm ở các điều kiện HP HT, bao gồm cả hoạt động trong hệ thống xử lý phía trên (nhiệt độ thấp).Mối quan tâm chính là sự kết tủa của chất ức chế cáu cặn trong đường ống sản xuất do tốc độ khí cao.Các thử nghiệm trong phòng thí nghiệm cho thấy chất ức chế cáu cặn có thể kết tủa và bám vào thành ống.Do đó, hoạt động của van an toàn có thể đánh bại rủi ro.
Kinh nghiệm cho thấy, sau vài tuần vận hành, đường ống dẫn hóa chất bị rò rỉ.Có thể theo dõi áp suất trong lòng giếng tại thiết bị đo bề mặt được lắp đặt trong đường mao dẫn.Dòng đã được phân lập để có được tính toàn vẹn tốt.
Dây chuyền bơm hóa chất đã được kéo ra khỏi giếng, mở và kiểm tra để chẩn đoán sự cố và tìm ra các nguyên nhân có thể dẫn đến sự cố.Như có thể thấy trong Hình.6, lượng kết tủa đáng kể đã được tìm thấy và phân tích hóa học cho thấy một số chất này là chất ức chế đóng cặn.Kết tủa nằm ở phớt và chốt và van không hoạt động được.
Sự cố van là do các mảnh vụn bên trong hệ thống van ngăn cản các van kiểm tra ăn vào bệ kim loại với kim loại.Các mảnh vụn đã được kiểm tra và các hạt chính được chứng minh là phoi kim loại, có thể được tạo ra trong quá trình lắp đặt đường ống mao dẫn.Ngoài ra, một số mảnh vụn màu trắng đã được xác định trên cả hai van kiểm tra, đặc biệt là ở mặt sau của van.Đây là phía áp suất thấp, tức là phía luôn tiếp xúc với chất lỏng trong giếng.Ban đầu, người ta cho rằng đây là mảnh vỡ từ giếng sản xuất do các van đã bị kẹt mở và tiếp xúc với chất lỏng trong giếng.Nhưng việc kiểm tra các mảnh vụn đã chứng tỏ là các polyme có tính chất hóa học tương tự như hóa chất được sử dụng làm chất ức chế cáu cặn.Điều này thu hút sự quan tâm của chúng tôi và Statoil muốn khám phá lý do đằng sau những mảnh vụn polyme này có trong đường mao dẫn.
Trình độ chuyên môn hóa học
Trong lĩnh vực HP HT có nhiều thách thức liên quan đến việc lựa chọn hóa chất phù hợp để giảm thiểu các vấn đề sản xuất khác nhau.Để đánh giá chất lượng của chất ức chế cáu cặn đối với lỗ phun liên tục, các thử nghiệm sau đây đã được thực hiện:
● Tính ổn định của sản phẩm
● Lão hóa nhiệt
● Kiểm tra hiệu suất động
● Khả năng tương thích với nước hình thành và chất ức chế hydrat (MEG)
● Kiểm tra vua súng tĩnh và động
● Nước thông tin tái hòa tan, hóa chất tươi và MEG
Hóa chất sẽ được tiêm với liều lượng định trước,nhưng sản xuất nước sẽ không nhất thiết phải là hằng số,tức là trượt nước.Ở giữa những con sên nước,khi hóa chất đi vào giếng,nó sẽ được đáp ứng bởi một nóng,dòng khí hydrocacbon chảy nhanh.Điều này tương tự như việc tiêm chất ức chế cáu cặn trong ứng dụng nâng khí (Fleming etal.2003). Cùng với
nhiệt độ khí cao,nguy cơ dung môi bị tước là rất cao và súng phun có thể gây tắc van phun.Đây là rủi ro ngay cả đối với các hóa chất được pha chế bằng dung môi có nhiệt độ sôi cao/áp suất hơi thấp và các Chất làm giảm áp suất hơi (VPD's) khác. Trong trường hợp tắc nghẽn một phần,dòng nước hình thành,MEG và/hoặc hóa chất mới phải có khả năng loại bỏ hoặc hòa tan lại hóa chất đã khử nước hoặc bị cô đặc.
Trong trường hợp này, một thiết bị thử nghiệm mới trong phòng thí nghiệm đã được thiết kế để tái tạo các điều kiện dòng chảy gần các cổng phun tại hệ thống sản xuất HP/HTg.Các kết quả từ các thử nghiệm súng động lực cho thấy rằng trong các điều kiện ứng dụng được đề xuất, sự thất thoát dung môi đáng kể đã được ghi lại.Điều này có thể dẫn đến vua súng nhanh và cuối cùng là chặn dòng chảy.Do đó, nghiên cứu đã chứng minh rằng tồn tại rủi ro tương đối đáng kể đối với việc bơm hóa chất liên tục vào các giếng này trước khi sản xuất nước và dẫn đến quyết định điều chỉnh các quy trình khởi động bình thường cho lĩnh vực này, trì hoãn việc bơm hóa chất cho đến khi phát hiện thấy sự đột phá của nước.
Chất lượng của chất ức chế cáu cặn đối với lỗ phun liên tục tập trung nhiều vào quá trình tước dung môi và súng của chất ức chế cáu cặn tại điểm phun và trong dòng chảy nhưng tiềm năng của súng trong chính van phun không được đánh giá.Van phun có thể bị hỏng do mất dung môi đáng kể và vua súng nhanh,Hình.6.Kết quả cho thấy điều quan trọng là phải có cái nhìn tổng thể về hệ thống;không chỉ tập trung vào những thách thức sản xuất,nhưng cũng có những thách thức liên quan đến việc tiêm hóa chất,tức là van phun.
Kinh nghiệm từ các lĩnh vực khác
Một trong những báo cáo ban đầu về các vấn đề với các đường phun hóa chất đường dài là từ các trường vệ tinh Gull fak sandVig dis (Osa etal.2001). Các đường phun dưới biển đã bị chặn khỏi sự hình thành hydrat trong đường do sự xâm nhập của khí từ các chất lỏng được tạo ra vào dòng qua van phun.Các hướng dẫn mới để phát triển các hóa chất sản xuất dưới biển đã được phát triển.Các yêu cầu bao gồm loại bỏ hạt (lọc) và bổ sung chất ức chế hydrat (ví dụ như glycol) vào tất cả các chất ức chế cặn gốc nước sẽ được tiêm vào các mẫu dưới biển.Ổn định hóa học,độ nhớt và khả năng tương thích (chất lỏng và vật liệu) cũng được xem xét.Những yêu cầu này đã được đưa sâu hơn vào hệ thống Statoil và bao gồm cả việc bơm hóa chất vào lỗ khoan.
Trong giai đoạn phát triển của Oseberg S hoặc mỏ, người ta đã quyết định rằng tất cả các giếng phải được hoàn thiện bằng hệ thống DHC I (Fleming etal.2006). Mục tiêu là ngăn chặn CaCO;nhân rộng ở ống trên bằng cách tiêm SI.Một trong những thách thức lớn đối với các đường phun hóa chất là đạt được sự giao tiếp giữa bề mặt và lỗ thoát nước.Đường kính trong của dây phun hóa chất thu hẹp từ 7mm xuống 0,7mm(ID) quanh van an toàn hình khuyên do hạn chế về không gian và khả năng vận chuyển chất lỏng qua phần này đã ảnh hưởng đến tỷ lệ thành công.Một số giếng khoan có đường bơm hóa chất đã được cắm,nhưng lý do không được hiểu.Các dòng chất lỏng khác nhau (glycol,thô thiển,ngưng tụ,xylen,chất ức chế quy mô,nước, v.v.) đã được thử nghiệm trong phòng thí nghiệm về độ nhớt và khả năng tương thích và được bơm xuôi và ngược dòng để mở các đường ống;Tuy nhiên,chất ức chế cặn mục tiêu không thể được bơm hết xuống van phun hóa chất.Hơn nữa,các biến chứng đã được nhìn thấy với sự kết tủa của chất ức chế quy mô phosphonate cùng với nước muối hoàn thành CaCl z còn lại trong một giếng và vua súng của chất ức chế quy mô bên trong giếng có tỷ lệ gasoil cao và lượng nước cắt thấp (Fleming etal.2006)
bài học kinh nghiệm
Phát triển phương pháp thử nghiệm
Các bài học chính rút ra từ sự cố của hệ thống DHC I liên quan đến hiệu quả kỹ thuật của chất ức chế cáu cặn chứ không liên quan đến chức năng và quá trình phun hóa chất.Topside injection và subsea injection hoạt động tốt ngoài giờ;Tuy nhiên,ứng dụng đã được mở rộng để phun hóa chất xuống hố mà không có bản cập nhật tương ứng của các phương pháp xác định hóa chất.Kinh nghiệm của Statoil từ hai trường hợp thực địa được trình bày là tài liệu quản lý hoặc hướng dẫn về chứng nhận hóa chất phải được cập nhật để bao gồm loại ứng dụng hóa chất này.Hai thách thức chính đã được xác định là i) chân không trong dây chuyền phun hóa chất và ii) khả năng kết tủa hóa chất.
Sự bay hơi của hóa chất có thể xảy ra trên đường ống sản xuất (như đã thấy trong trường hợp gun king) và trong ống tiêm (giao diện tạm thời đã được xác định trong trường hợp chân không) có nguy cơ các chất kết tủa này có thể di chuyển theo dòng chảy và vào van phun và tiếp tục vào giếng.Van phun thường được thiết kế với bộ lọc ngược dòng điểm phun,đây là một thử thách,như trong trường hợp kết tủa, bộ lọc này có thể bị tắc khiến van bị hỏng.
Các quan sát và kết luận sơ bộ từ các bài học kinh nghiệm dẫn đến một nghiên cứu trong phòng thí nghiệm rộng rãi về các hiện tượng.Mục tiêu tổng thể là phát triển các phương pháp đánh giá chất lượng mới để tránh các vấn đề tương tự trong tương lai.Trong nghiên cứu này, nhiều thử nghiệm khác nhau đã được thực hiện và một số phương pháp phòng thí nghiệm đã được thiết kế (được phát triển theo thứ tự) để kiểm tra các hóa chất liên quan đến các thách thức đã xác định.
● Tắc nghẽn bộ lọc và ổn định sản phẩm trong hệ thống kín.
● Ảnh hưởng của việc mất một phần dung môi đối với khả năng ăn mòn của hóa chất.
● Ảnh hưởng của việc mất một phần dung môi trong mao quản đối với sự hình thành chất rắn hoặc nút nhớt.
Trong quá trình thử nghiệm các phương pháp trong phòng thí nghiệm, một số vấn đề tiềm ẩn đã được xác định
● Bộ lọc bị tắc nhiều lần và độ ổn định kém.
● Hình thành chất rắn sau khi bay hơi một phần từ mao quản
● PH thay đổi do mất dung môi.
Bản chất của các thử nghiệm được tiến hành cũng đã cung cấp thêm thông tin và kiến thức liên quan đến những thay đổi về tính chất vật lý của hóa chất trong mao quản khi chịu các điều kiện nhất định,và điều này khác với các giải pháp số lượng lớn trong các điều kiện tương tự như thế nào.Công việc thử nghiệm cũng đã xác định được sự khác biệt đáng kể giữa chất lỏng số lượng lớn,pha hơi và chất lỏng còn lại có thể dẫn đến tăng khả năng kết tủa và/hoặc tăng khả năng ăn mòn.
Quy trình kiểm tra khả năng ăn mòn của chất ức chế cáu cặn đã được phát triển và đưa vào tài liệu quản lý.Đối với mỗi ứng dụng, thử nghiệm ăn mòn mở rộng phải được thực hiện trước khi có thể thực hiện tiêm chất ức chế cáu cặn.Gun king kiểm tra hóa chất trong dây chuyền tiêm cũng đã được thực hiện.
Trước khi bắt đầu đánh giá chất lượng của một hóa chất, điều quan trọng là phải tạo ra một phạm vi công việc mô tả các thách thức và mục đích của hóa chất.Trong giai đoạn đầu, điều quan trọng là phải xác định những thách thức chính để có thể chọn loại (các) hóa chất sẽ giải quyết vấn đề.Một bản tóm tắt các tiêu chí chấp nhận quan trọng nhất có thể được tìm thấy trong Bảng 2.
Định mức hóa chất
Đánh giá chất lượng hóa chất bao gồm cả thử nghiệm và đánh giá lý thuyết cho từng ứng dụng.Đặc điểm kỹ thuật và tiêu chí kiểm tra phải được xác định và thiết lập,ví dụ như trong HSE,khả năng tương thích vật liệu,độ ổn định của sản phẩm và chất lượng sản phẩm (hạt).Hơn nữa,điểm đóng băng,độ nhớt và khả năng tương thích với các hóa chất khác,chất ức chế hydrat,nước hình thành và chất lỏng sản xuất phải được xác định.Danh sách đơn giản hóa các phương pháp thử nghiệm có thể được sử dụng để xác định chất lượng hóa chất được đưa ra trong Bảng 2.
Liên tục tập trung và giám sát hiệu quả kỹ thuật,tỷ lệ liều lượng và thông tin HSE là rất quan trọng.Các yêu cầu của một sản phẩm có thể thay đổi một lĩnh vực hoặc một đời máy xử lý;thay đổi theo tốc độ sản xuất cũng như thành phần chất lỏng.Hoạt động tiếp theo với đánh giá hiệu suất,việc tối ưu hóa và/hoặc thử nghiệm các hóa chất mới phải được thực hiện thường xuyên để đảm bảo chương trình xử lý tối ưu.
Tùy thuộc vào chất lượng dầu,sản xuất nước và những thách thức kỹ thuật tại nhà máy sản xuất ngoài khơi,việc sử dụng hóa chất sản xuất có thể cần thiết để đạt được chất lượng xuất khẩu,yêu cầu quy định,và vận hành hệ thống lắp đặt ngoài khơi một cách an toàn.Tất cả các lĩnh vực đều có những thách thức khác nhau và các hóa chất sản xuất cần thiết sẽ khác nhau giữa các lĩnh vực và theo thời gian.
Điều quan trọng là tập trung vào hiệu quả kỹ thuật của hóa chất sản xuất trong một chương trình đánh giá chất lượng,nhưng nó cũng rất quan trọng để tập trung vào các tính chất của hóa chất,chẳng hạn như sự ổn định,chất lượng sản phẩm và khả năng tương thích.Khả năng tương thích trong cài đặt này có nghĩa là khả năng tương thích với chất lỏng,nguyên vật liệu và hóa chất sản xuất khác.Đây có thể là một thách thức.Không nên sử dụng một hóa chất để giải quyết một vấn đề để sau đó phát hiện ra rằng hóa chất đó góp phần hoặc tạo ra những thách thức mới.Có thể các đặc tính của hóa chất chứ không phải thách thức kỹ thuật mới là thách thức lớn nhất.
Yêu cầu đặc biệt
Các yêu cầu đặc biệt về lọc các sản phẩm được cung cấp phải được áp dụng cho hệ thống dưới đáy biển và cho lỗ phun liên tục.Bộ lọc và bộ lọc trong hệ thống phun hóa chất phải được cung cấp dựa trên thông số kỹ thuật trên thiết bị xuôi dòng từ hệ thống phun trên cùng,máy bơm và van phun,đến các van phun hạ cấp.Khi áp dụng việc phun hóa chất liên tục vào lỗ khoan, thông số kỹ thuật trong hệ thống phun hóa chất phải dựa trên thông số kỹ thuật có mức độ quan trọng cao nhất.Đây có thể là bộ lọc ở lỗ van phun.
thử thách tiêm
Hệ thống phun có thể ngụ ý khoảng cách 3-50 km của dòng chảy dưới đáy biển rốn và 1-3 km xuống giếng.Các tính chất vật lý như độ nhớt và khả năng bơm hóa chất rất quan trọng.Nếu độ nhớt ở nhiệt độ đáy biển quá cao, có thể gặp khó khăn khi bơm hóa chất qua đường phun hóa chất ở rốn dưới biển và đến điểm phun dưới biển hoặc trong giếng.Độ nhớt phải phù hợp với thông số kỹ thuật của hệ thống ở nhiệt độ bảo quản hoặc vận hành dự kiến.Điều này nên được đánh giá trong từng trường hợp,và sẽ phụ thuộc vào hệ thống.Vì bảng tốc độ phun hóa chất là một yếu tố quyết định thành công trong việc phun hóa chất.Để giảm thiểu nguy cơ tắc đường phun hóa chất,các hóa chất trong hệ thống này phải được ức chế hydrat (nếu có khả năng tạo hydrat).Khả năng tương thích với chất lỏng có trong hệ thống (chất lỏng bảo quản) và chất ức chế hydrat phải được thực hiện.Kiểm tra độ ổn định của hóa chất ở nhiệt độ thực tế (nhiệt độ môi trường thấp nhất có thể,nhiệt độ môi trường xung quanh,nhiệt độ dưới đáy biển,nhiệt độ phun) phải được thông qua.
Một chương trình rửa các dây chuyền phun hóa chất ở tần suất nhất định cũng phải được xem xét.Việc thường xuyên súc rửa đường phun hóa chất bằng dung môi có thể mang lại hiệu quả phòng ngừa,glycol hoặc hóa chất tẩy rửa để loại bỏ cặn có thể có trước khi tích tụ và có thể gây tắc đường dây.Dung dịch hóa chất được chọn của chất lỏng xả phải làtương thích với hóa chất trong đường tiêm.
Trong một số trường hợp, dây phun hóa chất được sử dụng cho một số ứng dụng hóa học dựa trên những thách thức khác nhau trong suốt thời gian sử dụng và điều kiện chất lỏng.Trong giai đoạn sản xuất ban đầu trước khi nước đột phá, những thách thức chính có thể khác với những thách thức trong giai đoạn cuối đời thường liên quan đến việc tăng sản lượng nước.Để thay đổi từ chất ức chế gốc dung môi không chứa nước như chất ức chế ene nhựa đường sang hóa chất gốc nước như chất ức chế cáu cặn có thể gây ra những thách thức về khả năng tương thích.Do đó, điều quan trọng là phải tập trung vào khả năng tương thích, chất lượng và cách sử dụng các miếng đệm khi có kế hoạch thay đổi hóa chất trong dây chuyền phun hóa chất.
Nguyên vật liệu
Về khả năng tương thích vật liệu,tất cả các hóa chất phải tương thích với con dấu,chất đàn hồi,gioăng và vật liệu cấu tạo dùng trong hệ thống phun hóa chất và nhà máy sản xuất.Nên xây dựng quy trình kiểm tra khả năng ăn mòn của hóa chất (ví dụ như chất ức chế cáu cặn có tính axit) đối với lỗ phun liên tục.Đối với mỗi ứng dụng, thử nghiệm ăn mòn mở rộng phải được thực hiện trước khi có thể thực hiện việc bơm hóa chất.
Cuộc thảo luận
Những ưu điểm và nhược điểm của việc phun hóa chất xuống lỗ liên tục phải được đánh giá.Tiêm liên tục chất ức chế cáu cặn để bảo vệ DHS Vor ống sản xuất là một phương pháp tao nhã để bảo vệ giếng khỏi cáu cặn.Như đã đề cập trong bài báo này, có một số thách thức với việc phun hóa chất xuống lỗ liên tục,tuy nhiên để giảm rủi ro, điều quan trọng là phải hiểu các hiện tượng liên quan đến giải pháp.
Một cách để giảm rủi ro là tập trung vào phát triển phương pháp thử nghiệm.So với phun hóa chất trên mặt hoặc dưới đáy biển, có những điều kiện khác nhau và khắc nghiệt hơn ở dưới giếng.Quy trình đánh giá chất lượng hóa chất để bơm liên tục hóa chất xuống hố khoan phải xem xét những thay đổi này trong điều kiện.Việc xác định chất lượng của hóa chất phải được thực hiện theo vật liệu mà hóa chất có thể tiếp xúc.Các yêu cầu về kiểm định và thử nghiệm khả năng tương thích ở các điều kiện sao chép càng gần càng tốt các điều kiện vòng đời giếng khác nhau mà các hệ thống này sẽ hoạt động phải được cập nhật và triển khai.Việc phát triển phương pháp thử nghiệm phải được phát triển hơn nữa để thử nghiệm thực tế và đại diện hơn.
Ngoài ra,sự tương tác giữa các hóa chất và thiết bị là điều cần thiết để thành công.Việc phát triển các van phun hóa chất phải tính đến các đặc tính hóa học và vị trí của van phun trong giếng.Nó nên được xem xét bao gồm các van phun thực như là một phần của thiết bị thử nghiệm và để thực hiện thử nghiệm hiệu suất của chất ức chế cáu cặn và thiết kế van như một phần của chương trình đánh giá chất lượng.Để đủ điều kiện chất ức chế quy mô,trọng tâm chính trước đó là các thách thức về quy trình và hạn chế quy mô,nhưng sự ức chế quy mô tốt phụ thuộc vào việc tiêm ổn định và liên tục.Nếu không được bơm ổn định và liên tục, khả năng mở rộng quy mô sẽ tăng lên.Nếu van phun chất ức chế cáu cặn bị kẹt và không có chất ức chế cáu cặn nào được bơm vào dòng chất lỏng,giếng và van an toàn không được bảo vệ khỏi cặn và do đó quá trình sản xuất an toàn có thể bị nguy hiểm.Quy trình đủ điều kiện phải quan tâm đến những thách thức liên quan đến việc tiêm chất ức chế cáu cặn bên cạnh những thách thức về quy trình và hiệu quả của chất ức chế cáu cặn đủ tiêu chuẩn.
Cách tiếp cận mới liên quan đến một số ngành và sự hợp tác giữa các ngành và trách nhiệm tương ứng phải được làm rõ.Trong ứng dụng này, hệ thống xử lý bên trên,các mẫu dưới biển và thiết kế và hoàn thiện giếng có liên quan.Mạng lưới đa lĩnh vực tập trung vào việc phát triển các giải pháp mạnh mẽ cho hệ thống phun hóa chất là rất quan trọng và có thể là con đường dẫn đến thành công.Giao tiếp giữa các ngành khác nhau là rất quan trọng;đặc biệt là sự liên lạc chặt chẽ giữa các nhà hóa học có quyền kiểm soát các hóa chất được áp dụng và các kỹ sư giếng có quyền kiểm soát thiết bị được sử dụng trong giếng là rất quan trọng.Để hiểu những thách thức của các lĩnh vực khác nhau và học hỏi lẫn nhau là điều cần thiết để hiểu được sự phức tạp của toàn bộ quá trình.
Phần kết luận
● Phun liên tục chất ức chế cáu cặn để bảo vệ DHS Vor ống sản xuất là một phương pháp tao nhã để bảo vệ giếng khỏi cáu cặn
● Để giải quyết những thách thức đã xác định,các khuyến nghị sau đây là:
● Phải thực hiện quy trình thẩm định chuyên dụng của DHCI.
● Phương pháp định tính van phun hóa chất
● Phương pháp kiểm tra và xác định chức năng hóa học
● Phát triển phương pháp
● Thử nghiệm vật liệu liên quan
● Sự tương tác đa lĩnh vực trong đó giao tiếp giữa các lĩnh vực khác nhau có liên quan là rất quan trọng để thành công.
Sự nhìn nhận
Tác giả muốn cảm ơn Statoil AS A đã cho phép xuất bản tác phẩm này và Baker Hughes và Schlumberger đã cho phép sử dụng hình ảnh trong Hình.2.
danh pháp
(Ba/Sr)SO4=bari/stronti sunfat
CaCO3=canxi cacbonat
DHCI=phun hóa chất xuống lỗ
DHSV=van an toàn hạ cấp
vd=ví dụ
GOR=tỷ lệ gasoil
HSE=môi trường an toàn sức khỏe
HPHT = nhiệt độ cao áp suất cao
ID = đường kính trong
tức là = đó là
km=km
mm=milimet
MEG=mono etylen glycol
mMD=m độ sâu đo được
OD=đường kính ngoài
SI = chất ức chế quy mô
mTV D = mét tổng độ sâu dọc
U-tube=Ống hình chữ U
VPD=giảm áp suất hơi
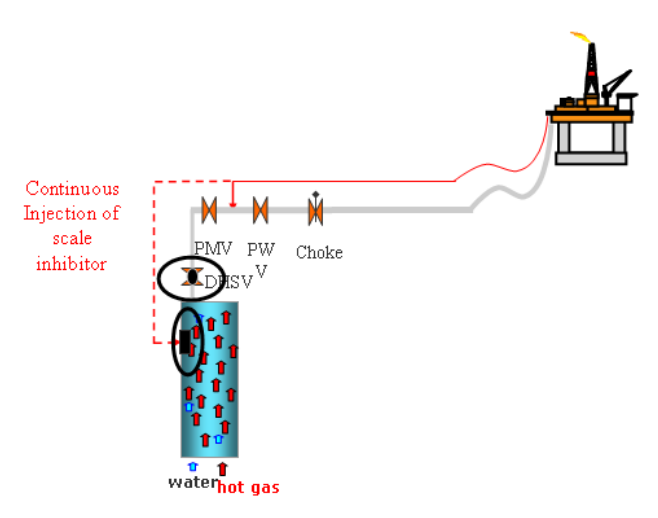
Hình 1. Tổng quan về hệ thống phun hóa chất dưới đáy biển và lỗ khoan trong trường không điển hình.Phác thảo quá trình bơm hóa chất lên dòng DHSV và những thách thức dự kiến liên quan.DHS V=van an toàn hạ cấp, PWV=van cánh quy trình và PM V=van chính quy trình.
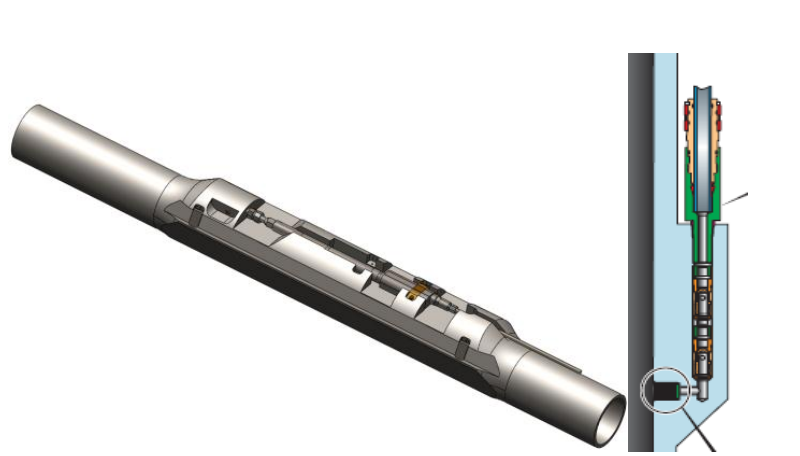
Hình 2. Bản phác thảo hệ thống phun hóa chất không điển hình trong hố khoan với trục gá và van.Hệ thống được nối với ống góp bề mặt, được đưa qua-và nối với giá treo ống ở mặt hình khuyên của ống.Theo truyền thống, trục gá phun hóa chất được đặt sâu trong giếng với mục đích bảo vệ hóa chất.
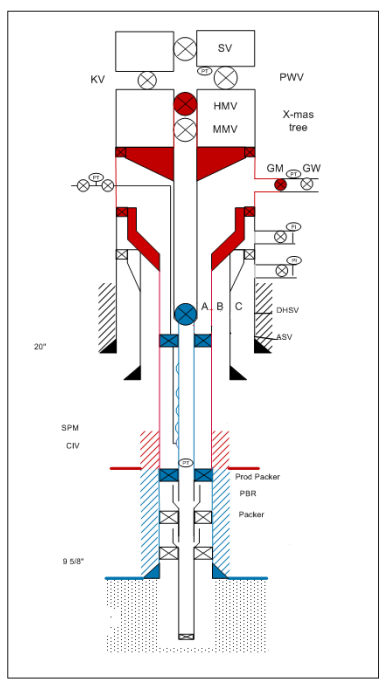
Hình 3. Sơ đồ rào chắn giếng điển hình,trong đó màu xanh đại diện cho đường bao rào chắn giếng chính;trong trường hợp này là ống sản xuất.Màu đỏ đại diện cho phong bì hàng rào thứ cấp;vỏ bọc.Ở phía bên tay trái được chỉ định tiêm hóa chất, vạch đen có điểm tiêm vào ống sản xuất trong khu vực được đánh dấu màu đỏ (hàng rào thứ cấp).
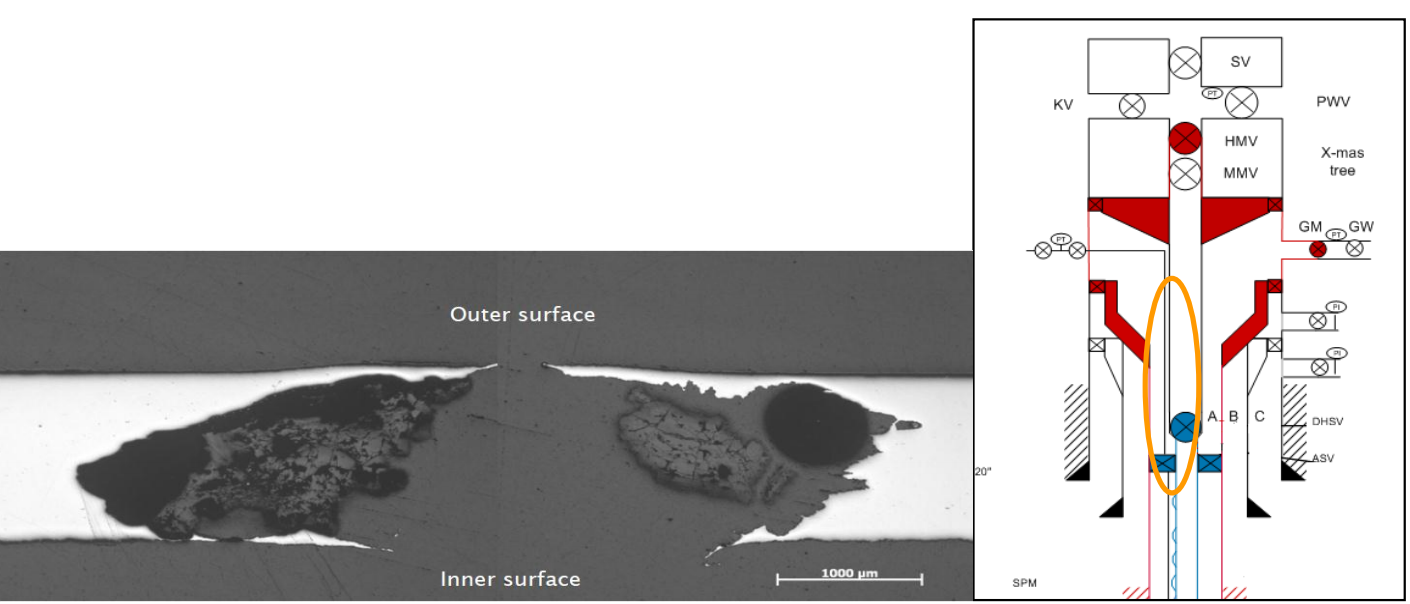
Hình 4. Lỗ rỗ được tìm thấy ở phần trên của đường tiêm 3/8”.Khu vực này được thể hiện trong bản phác thảo sơ đồ rào chắn giếng không điển hình, được đánh dấu bằng hình elip màu cam.
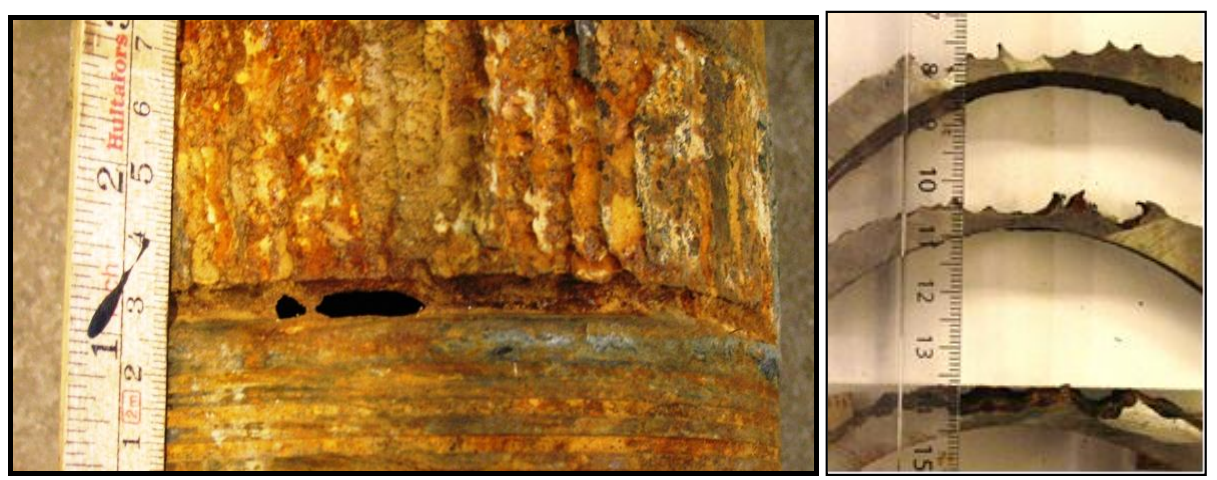
Hình 5. Sự tấn công ăn mòn nghiêm trọng trên ống Chrome 7” 3%.Hình vẽ cho thấy sự tấn công ăn mòn sau khi chất ức chế cáu cặn được phun từ dây chuyền phun hóa chất có rỗ vào đường ống sản xuất.
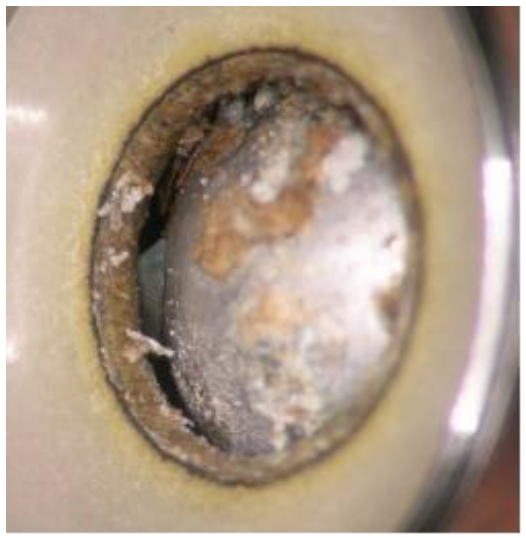
Hình 6. Các mảnh vụn được tìm thấy trong van phun hóa chất.Mảnh vụn trong trường hợp này là phoi kim loại có thể từ quá trình lắp đặt cùng với một số mảnh vụn màu trắng.Kiểm tra các mảnh vụn màu trắng được chứng minh là các polyme có tính chất hóa học tương tự như hóa chất được tiêm
Thời gian đăng: 27-04-2022